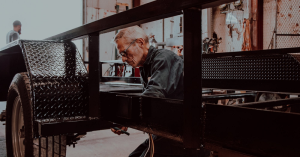
Our trailer parts expert will answer your inquiries within 12 hours.
Tow-Max is a trusted supplier of trailer parts in China, known for its huge variety of products and one-stop services. We have been supplying customers from Australia, South America, the USA, and the Middle East. Our business partners are located in Sydney, Melbourne, Adelaide, Mexico City, Dubai, etc.
No.163-1, Shang yang Road, Dongqian Lake Industrial Zone, Ningbo, 315121, Zhejiang, China
+86-574-8786-2718
+86-574-8786-2717
sales(at)soaringtrailerparts.com
©Copyright 2020. Tow-Max. All rights reserved. Powered by MML.